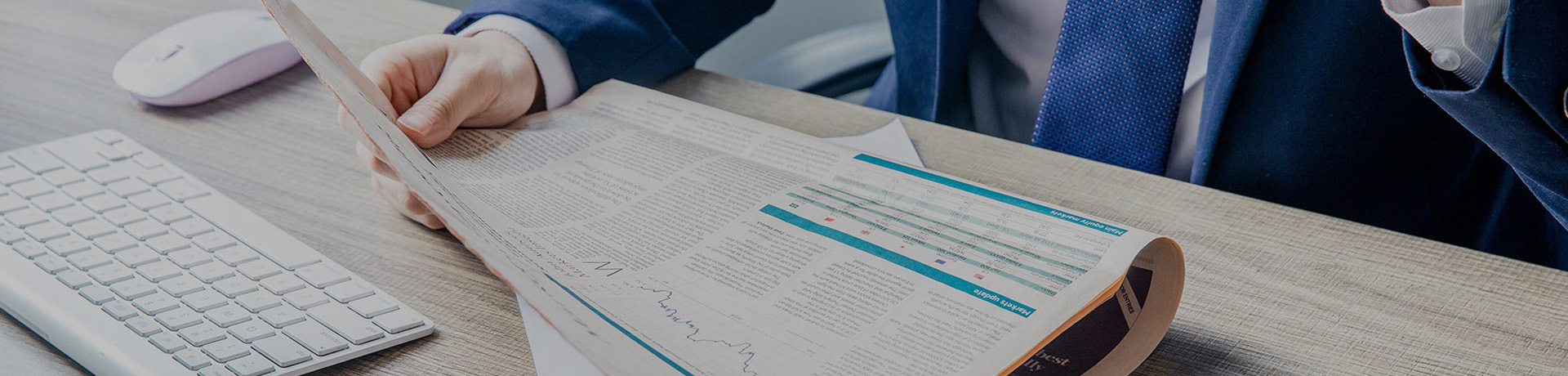
News Center
Refractory castable such construction is in line with national standards!
Release time:
2021-11-12
In the construction of refractory castables, many construction teams do not have professional construction qualifications, and project delays or material waste caused by unqualified construction quality occur from time to time. In fact, in the national standards, the construction of refractory castable, maintenance, mold removal and construction of refractory castable prefabricated parts, have made a very clear specification requirements. Specific as follows:
1. Waterproof measures shall be taken for the surface of thermal insulation masonry in contact with refractory castable.
2. The refractory castable shall be stirred by a forced mixer. Stirring time and the amount of liquid should be in accordance with the product instructions. When changing the material grade, the mixing tool, hopper and weighing container should be cleaned.
3. The stirred refractory castable shall be poured within 30min or within the specified time according to the product instruction. The initially set refractory castable shall not be used.
4. The steel bars or metal embedded parts in the refractory castable shall be located on the non-heated surface. The expansion buffer layer shall be set at the contact part between the steel bar or metal embedded parts and the refractory castable according to the design regulations.
5. The setting of the expansion joint of the integral pouring refractory lining shall comply with the design regulations. When there is no provision for the expansion joint in the design, it can be set according to the test results of GB/T7320, the current national standard "thermal expansion test method for refractory materials. For clayey or high-alumina refractory castables, etc., the following data can also be used for the average value of lining expansion joints per meter length:
1 Clay refractory castable is 4mm6mm;
2 Aluminate cement refractory castable is 6mm 8mm;
3 phosphate refractory castable is 6mm 8mm;
4 The water glass refractory castable is 4mm6mm;
5 Portland cement refractory castable is 5mm 8mm.
6. The refractory castable shall be vibrated and compacted. Vibrating rod or plate vibrator should be used for vibrating machine. When using a vibrating rod, the thickness of the casting layer should not exceed 1.25 times the length of the working part of the vibrating rod; when using a flat vibrator, its thickness should not exceed 200mm.
7. The heat-insulating refractory castable shall be tamped manually. When mechanical vibration is used, segregation and bulk density increase shall be prevented.
8. The construction of refractory castable shall be carried out continuously. Before the initial setting of the former refractory castable, the secondary refractory castable shall be poured. Intermittent time exceeding the initial setting time shall be handled according to the requirements of construction joints. Construction joints shall be left at the center line of the same row of anchor bricks.
9. The refractory castable shall be maintained according to the method specified in the design after construction. If there is no design provision, the provisions in Table 1 can be followed. The refractory castable shall not be subjected to external force and vibration during curing.
10. The load-bearing formwork shall be removed after the refractory castable reaches more than 70% of the design strength. Hot hard refractory castables shall be baked to the specified temperature and then removed.
11, refractory castable on-site pouring quality, for each brand or the same mix ratio should be every 20m3 for a batch of retained test blocks for inspection, less than this number also for a batch of inspection. When the same brand or the same mix ratio is used for multiple construction, the test block shall be retained for each construction. The test block shall be tested according to the current relevant national standards.
12. The surface of the refractory castable lining may have slight network cracks, but there shall be no cracks, holes, spalling and other defects.
13. The surface of the prefabricated refractory castable transported to the construction site shall include the following contents:
1 Production unit imprint;
2 Quality inspection mark;
3 There are part numbers consistent with the construction drawings on three different surfaces;
4 Signs of lifting points;
5 Date of production.
14. Precast parts of refractory castable shall not be stacked in the open air. When outdoor stacking is required, rainproof and moisture-proof measures shall be taken.
15. When stacking the precast piece of refractory castable, the position and method of support shall conform to the stress of the precast piece. The top precast piece is not suitable for stacking. When stacking is required, it shall not be directly stacked on the hanging brick of the top precast piece.
16. The prefabricated parts of refractory castable shall be provided with hoisting rings. When temporary lifting tools are required, the hoisting requirements shall be met. When lifting the precast piece of refractory castable, the strength of the precast piece shall reach the strength specified in the design. The precast piece of refractory castable shall be lifted gently.
17, for the use of hanging brick as a force transmission system of the furnace top precast, in the process of lifting, installation, each hanging brick should be balanced force, shall not be damaged.
18, refractory castable prefabricated masonry gap width and treatment should be in accordance with the design provisions.
Related News
2021-11-12