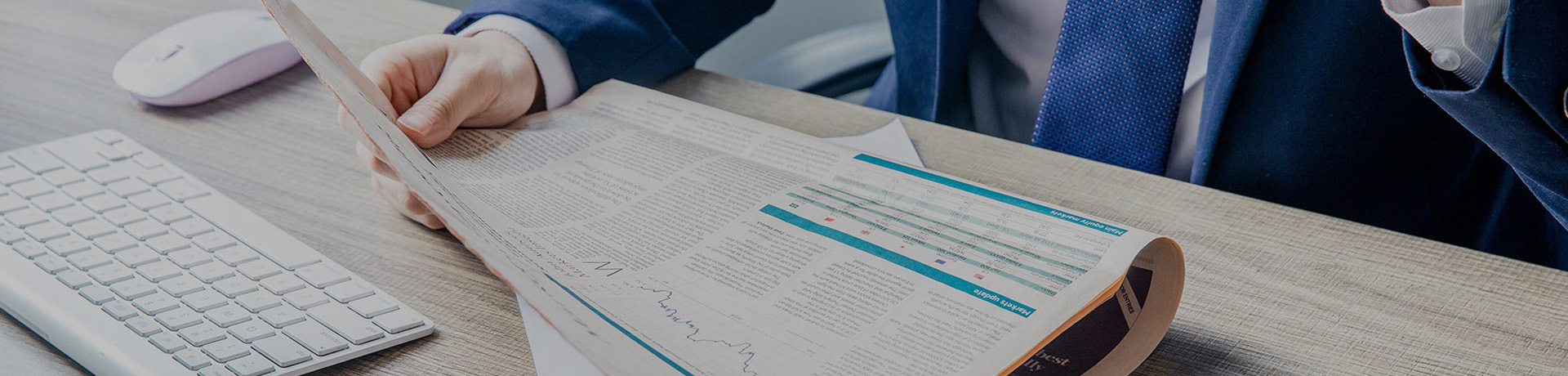
News Center
Mullite castable base formula
Release time:
2021-11-12
The basic formula of mullite castable is 68.0% of 7~0mm pyrocarbides, 23.0% of alumina micropowder, 3.7% of silica micropowder, 5% of calcium aluminate cement, 02% of compound water reducing agent and 0.1% of anti-cracking fiber. The basic formula is recorded as 0# formula. On the basis of 0# formula, 2.5%, 5.0%, 7.5% and 10% of silicon carbide are introduced respectively, and the dosage of alumina micropowder is reduced accordingly, respectively recorded as 1#~ 4# formula. First of all, the formula material is placed in the mixing tank, and 6% distilled water is added for mixing, and the mixing time is 3min. After mixing, the material vibration is divided into two kinds of samples, one is used for normal temperature performance detection (sample size is 40mm × 40mm × 160mm), and the other is used for alkali resistance test of pile pot sample (outer contour is 70mm × 70mm inner contour b25mm × 30mm). After the sample is cured at room temperature for 48h, the heat treatment is carried out at 110 ℃ for 24h. After heat treatment at 110 ℃, the pot samples and some strip samples were heat treated at 1100 ℃ for 3h. Finally, the alkali corrosion resistance test is carried out. 20g of analytically pure potassium carbonate is placed in the storage yard sample, heated to 1100 ℃ for 2h in a high-temperature furnace with a temperature rising system of 5 ℃/min, and the alkali corrosion resistance sample of castable is cooled to room temperature with the furnace.
2.3 characterization
First, the normal temperature properties of the samples after heat treatment at 110 ℃ and 1100 ℃ were detected: including normal temperature compressive strength, normal temperature flexural strength, linear change rate and volume density after burning. Secondly, the Dutch xPert-MpD-type X-ray diffractometer (Cuk radiation, tube pressure 40kv, tube flow: 40mA, step 0.02 ° scanning speed of 40-min-1, scanning range 15o ~ 65.) The phase composition of the sample after heat treatment at 1100 ℃ and the sample resistant to alkali erosion was analyzed. The chemical compositions of the heat-treated samples and alkali-resistant samples were analyzed by X-ray fluorescence spectrometry. The micro-morphology of the fracture surface of the burned sample was observed with a scanning electron microscope of Japan Electronic ISM6480LV.
Related News
2021-11-12